Starting with break through innovation, manufacturing full custom skis off-grid, combined with incremental improvement, we've developed technology for building skis that feel alive, highly responsive, and fast.
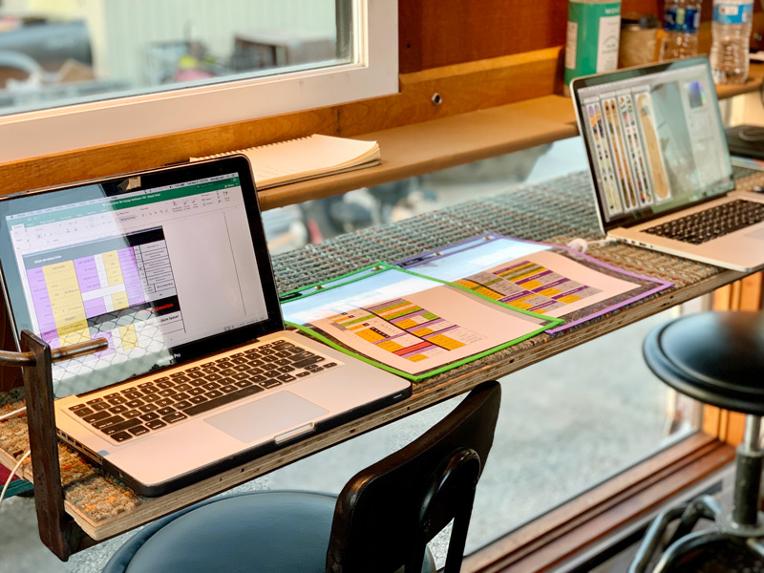
We developed our ski design software and graphic design protocol from the ground up and in-house. As we've learned more about the nuance of ski design, we've upgraded our software to give more accurate outputs and provide us with critical information regarding the build process.
Feedback from client performance evaluations can be put into our formula's in a timely manner. This allows us to design and build at the cutting edge.
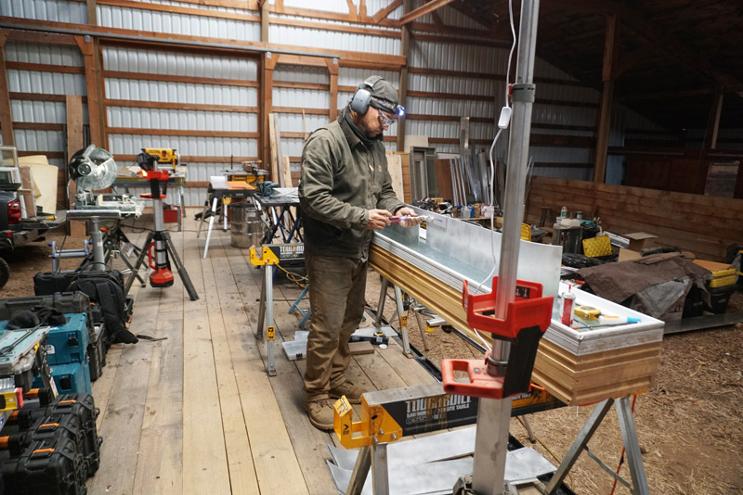
Bend, OR. For 4 years we worked in this barn and built 3 factories and Kristin's restaurant, House in the Fields. We hosted numerous workshops and built a number of custom skis. The majority of our factories are built on trailered platforms. This allows for zero rent and mobility. Manufacturing located in nature, or close to, with lots of natural light and beautiful views, feeds the creative and innovative part of who we are.
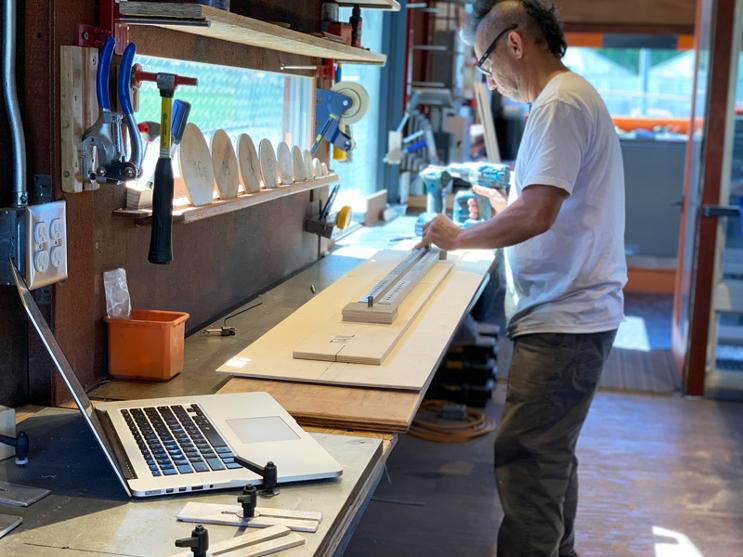
For better or worse, I don't use notes, drawings, or plans when building the factory envelope and tooling. Each time we approach building a new tool we have an opportunity to rethink it completely. How to fulfill its purpose with greater precision and higher efficiencies? But most importantly, is it intuitive? Can a student in a high school, Build Your Own Skis Workshop learn how to use it safely and then teach their fellow students how to use it in short order. We believe in competitive American manufacturing. We believe in order to compete we needed to rethink everything and do this often.
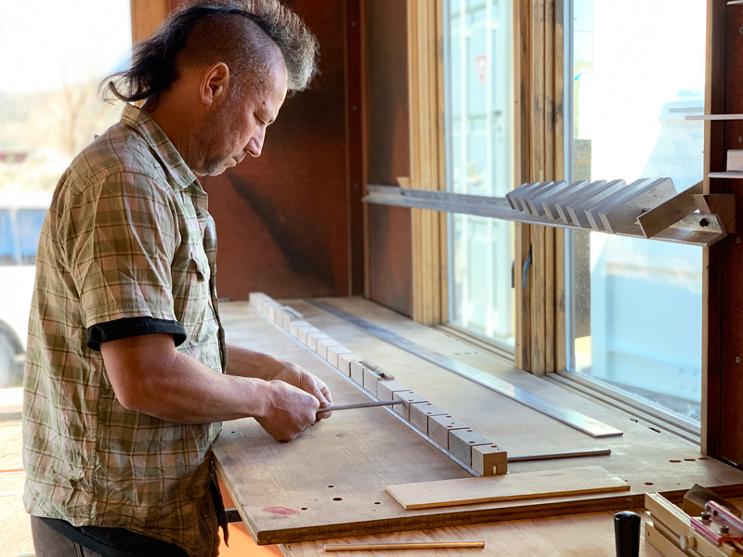
We use a lot of glass in our factory envelopes. Natural light and looking out at the long view, the setting sun, the moon, keeps our work in perspective. It seems to encourage us to do all we can, the best we can.
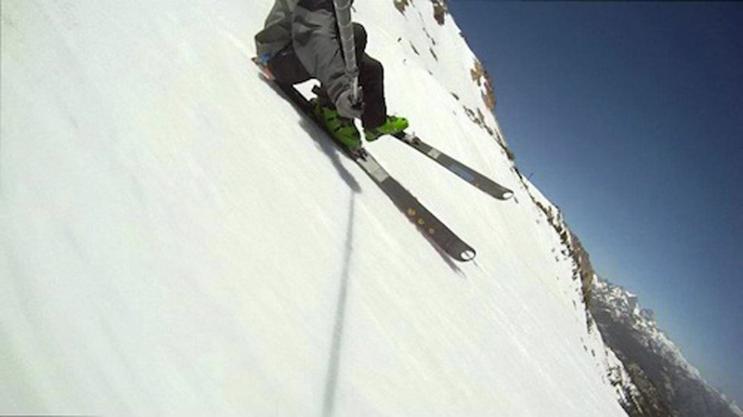
Testing skis is a blast. This is a full carbon "attack" build. Very light, highly responsive and torsionally rigid. I film a lot and review the footage to try to really understand what the skis were doing and how they were accomplishing it. When you're at the cutting edge, a lot of things are unknown. When you're willing to push the envelope it's entirely possible that things will fall apart, break. But this is what being alive is all about and then taking that experience and the information back into the factory to make a new generation of high performing skis.
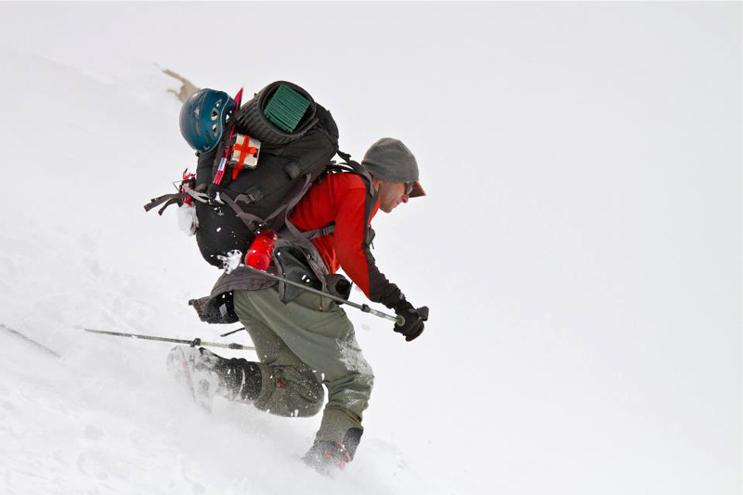
There are two things that we are really proud of at Community Skis; First, we can contribute to a persons education and make a meaningful contribution. Second, we can be a part of our clients passion and love of skiing.
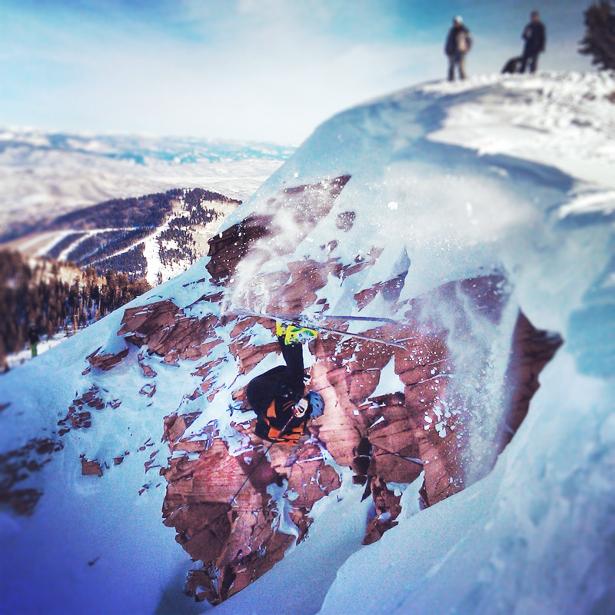
Each time a ski broke, we did a comprehensive analysis. A key understanding developed and we called it "load point failure". Typically a load is dispersed over an axial plane, but when it loads and is isolated in a particular section, that section is prone to failure. From this, we learned to reinforce these critical sections and allow for compression or tension to travel over the complete ski without loading. Most skis have overkill. They are not engineered, they're built. But understanding what's necessary in regards to reinforcement and what's overkill is specific to full custom.
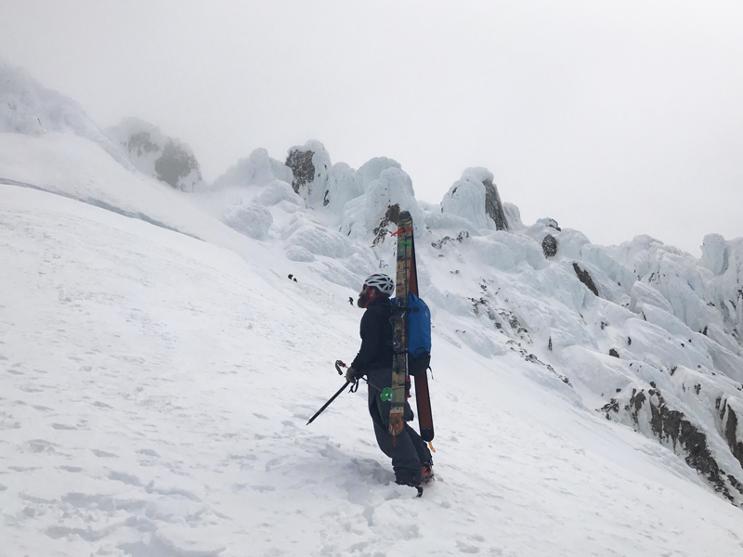
When things go sideways, we always try to remember this feeling. Matt, a teacher at Colorado Rocky Mountain School, had these skis built in a 12 student, on-campus workshop.
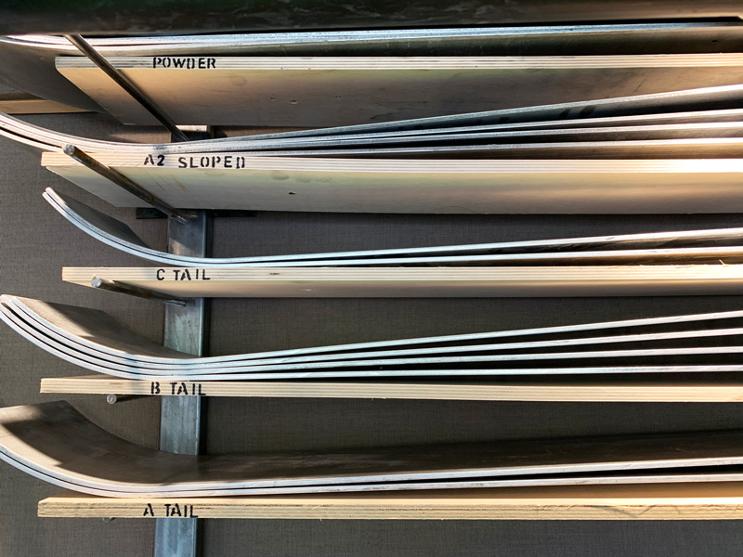
Our cassette stock, what we build the ski on, is 3/16th inch 50/52 quarter hardened aluminum. We roller-bend it in house on a 2" roller-bender I've had for over 30 years. Building full custom skis is limited by your tooling and your design process. We take into account material selection, depth of understanding in composites, material science, client ski styles, translating them into numeric values and then being meticulous through out the build process to meet specification and tolerance. Our tooling package allows us to build in 2cm increments for length, 2mm increments in regards to widths, camber/rocker profiles to an infinite degree and generate flex patterns that are entirely specific to your weight, how you ski and type of snow.
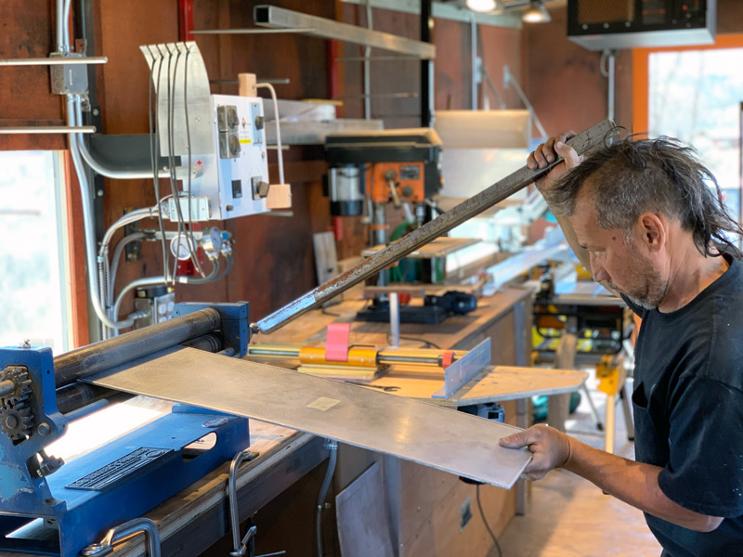
The manufacturing classrooms we build for public schools incorporates snowboards, full custom. The cassettes we build have 3 parts. They're designed like a dinner table in that you can add a leaf when you need to increase size. But each cassette has an array of leaves, from 2cm up to 20cm. This allows a 162cm cassette to incrementally expand to 182cm. So instead of having 10 cassettes for each of these lengths, we simply have one.
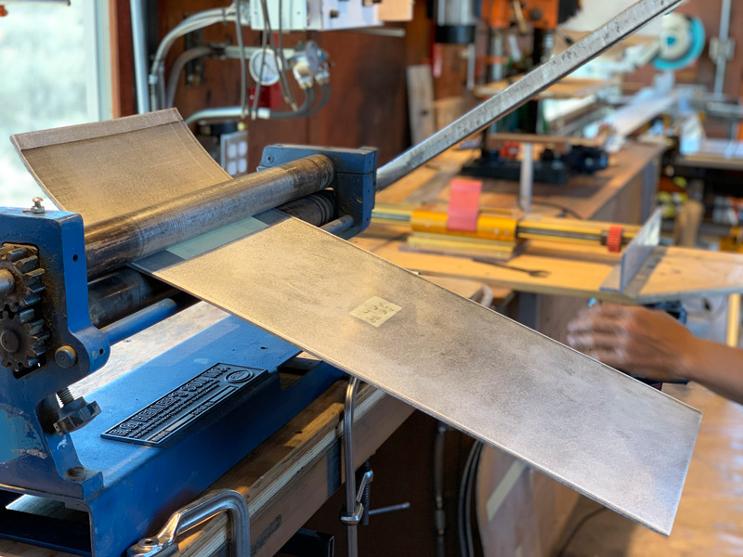
There's a magic, something almost profound in working with materials. Transforming them into tooling, paying attention to how they're changing as you work them still remains a wonder to me.
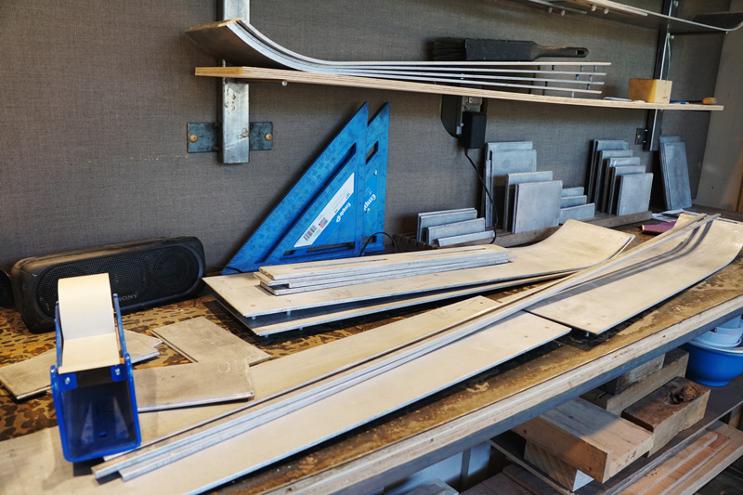
Neuro science is starting to understand how the mind works, how the creative process comes into being, how ideas are formed. When an idea emerges, Kristin and I will have a discussion, do our best to listen to each other, explore the potential of the idea, understand the resources required to bring it to fruition and the energy, effort and time. That's just the beginning. Then you got to make it happen. If it's a breakthrough innovation, be prepared. People are going to try and kick you down. But get over it, stay the course. That's not what's important. What is important is that you have an idea, you have a partner and you're willing to do the work. This picture shows a thousand steps or more to develop the parts for the adjustable cassettes. This idea in particular has produced phenomenal results. Of course, not all of them do. So what?
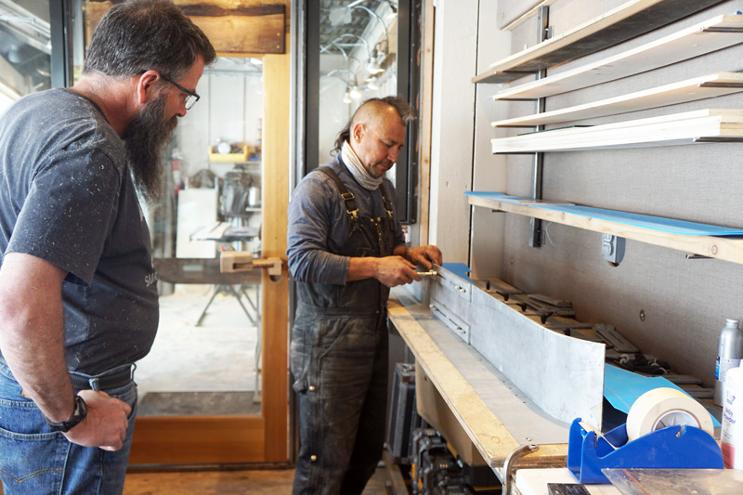
A lot of what we do is sharing what we do. This is a high school teacher from Colorado who came down to Oregon for a Build-Your-Own-Skis-Workshop. This is not uncommon. Teachers from all over the United States and Canada have taken this path. We share our technology and load them with all the insight that we can. It might be a year, two, three before we hear from them again. But they'll send us pictures of their students building skis. There's no imagining what it means to give your blood sweat and tears away. Your ideas, your competitive edge, your proprietary knowledge. But when you understand the question, what's meaningful? and when you grapple with the answer and you want to live a meaningful life, giving away seems vastly more meaningful than holding on.

Camber/rocker profiles have a significant influence on ski performance. Using traditional press technology you're essentially stuck with a handful of profiles because of the girth and cost of creating each throat required for each different profile. This is one of 100 reasons why modern ski manufacturing is cookie-cutter. One like the other, like the other. Full custom required breakthrough innovations but keeping it simple, efficient, reproducible with predictable outcomes, able to be used by high school students in short order, makes custom manufacturing possible and affordable.
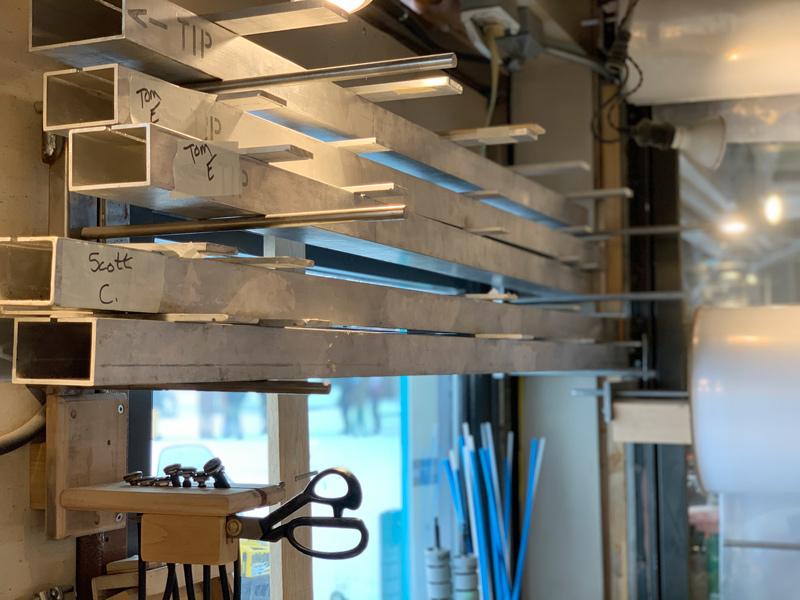
Putting things back is something most people don't do. So how to create a factory where everything goes back where it needs to, became an art for us. We took into account how the body lifts things, brings things down, articulates. We combined that with aesthetics so things in their place looked really good and we created an environment where you and your teammates would encourage each other if need be. But it's comforting to know that good design is precisely that. Good design because it works.
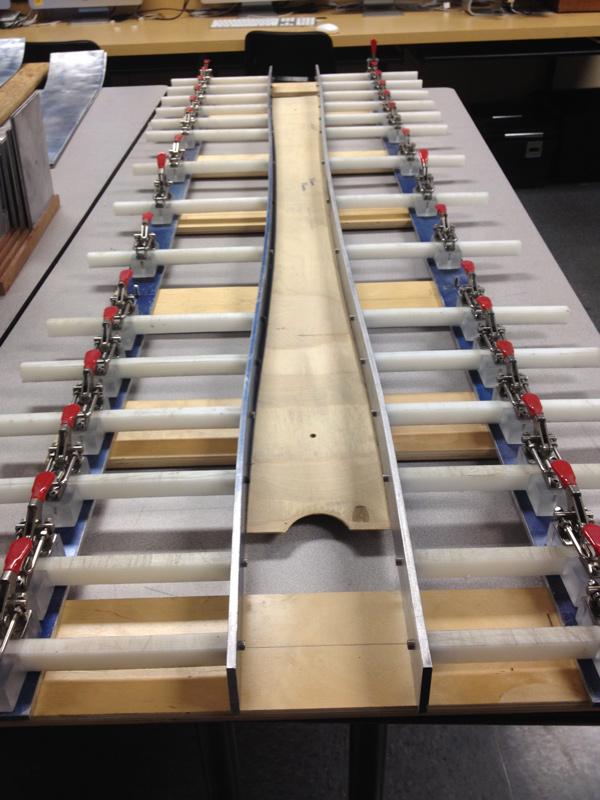
To create the shape of each custom ski, we invented the "rail package". This in tandem with calibration blocks and our software's "shop copy", we are able to shape and side profile the core start to finish in less than 7 mins. This is considerably faster than CNC due to both its fast setup and significantly faster feed rates. Every factory we've built, which is in excess of 15, the rail package has been incrementally upgraded. At this point, it reflects simplicity of design, accuracy in repeatability and extremely tight tolerances (sub millimeter). And to put things into perspective, the slower CNC machine probably cost more than our complete factory based on our tooling and process.
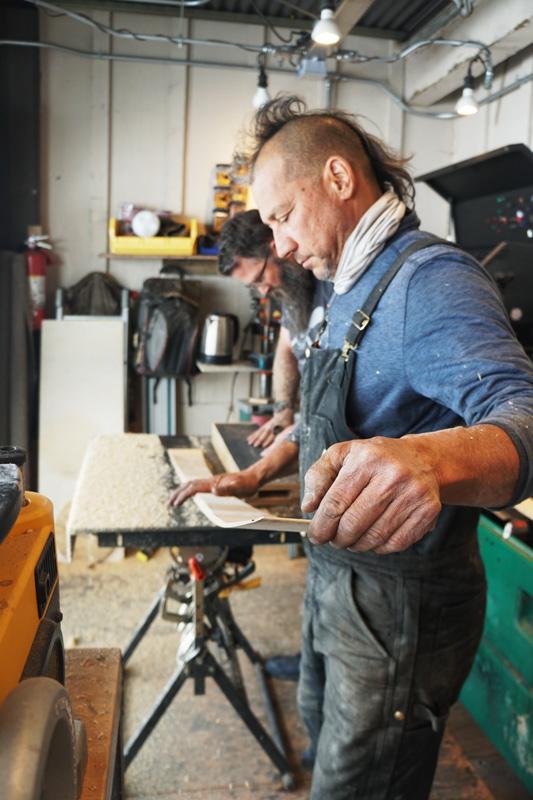
The Design Request Form gives us a lot of information and the shop copy, generated by our software, presents us with the numerical values that are derived from the answers you give. How much you weight and the type of ski we're building for you, dictates the length of taper in the core, which is responsible for pattern of flex and core termination thickness which determines overall stiffness. The termination thickness along with the fiberglass/carbon package used to build the skis, act in unison, developing the strength, resilience and reinforcement. Couple this with camber, which induces liveliness and responsiveness across the fall line on steep, deep carves and we begin to develop the interrelations of the components/materials along with the mill work that generate full custom.
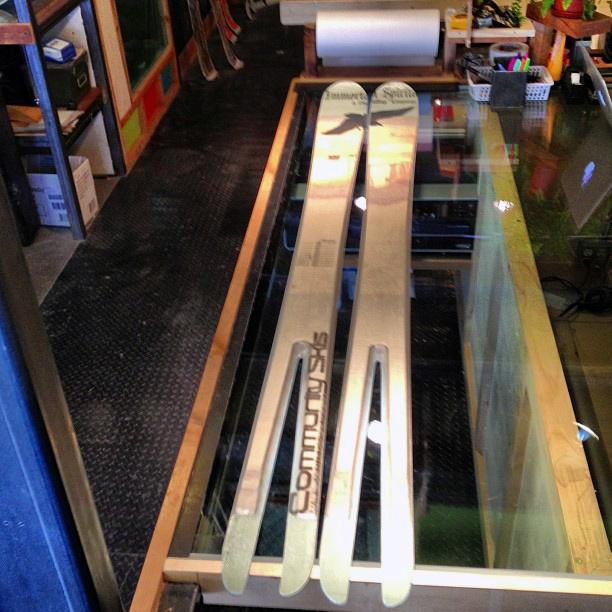
The ideas we are currently working with are embedded technologies such as location chips, antenna's for cell service, fabric type solar panel top-skins for extended backcountry touring, and high density polycarbonate (battle tank portal material) for underfoot sections to hold up to park abuse. The skis you are looking at here have insane performance characteristics. The deep swallow tails are a multi wrapped torsion box, so they lock and load at high speed deep carving. By removing the mass in the tail an in-snow ski geometry is developed which essentially drops the tail forcing the tip to porpoise so these are a true powder ski that out carves any dedicated carving ski. Because our factories don't have rent, they're mobile, and because our factories are considerably less to build than the typical CNC with press stack (the common factory) we are able to utilize monetary and time resources to prototype and develop. There were times when we had to pay rent. It was a beautiful factory. A live/work space in Mammoth, but honestly, paying rent sucks. We'd rather work to prototype than work to pay rent.
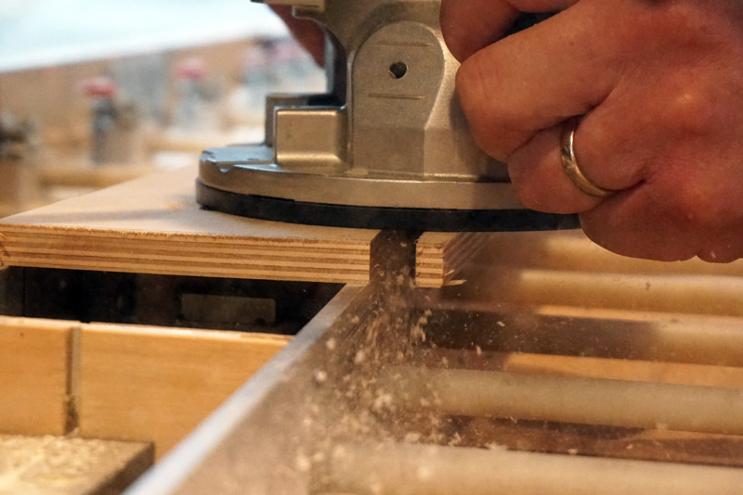
It is part of human nature to use our hands. Our brains are wired this way. Fortunately there is a great enjoyment in doing so and if you do it for a living, over time, your skills improve. Society use to reflect this process and it started with the apprentice, then the journeyman, and then master. We respect this process. We believe it can still make a difference.
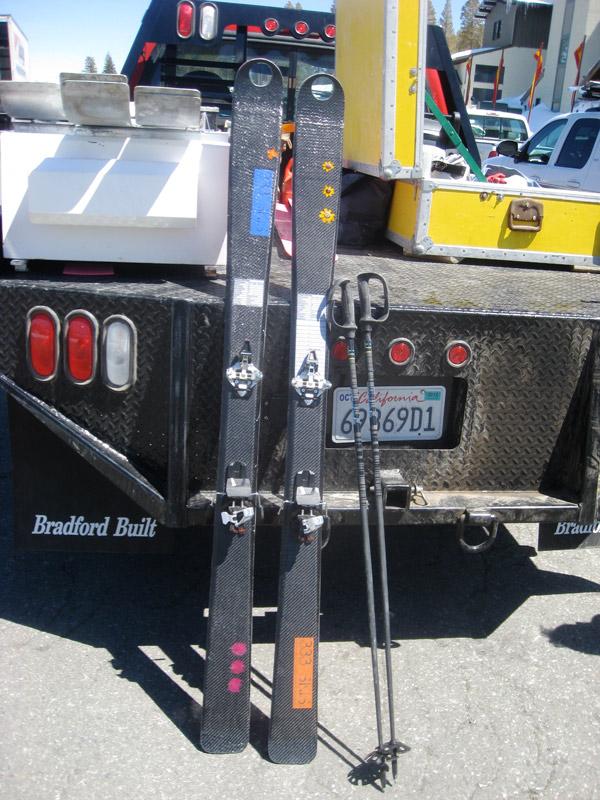
For nearly 4 years, Kristin and I were based in a caldera behind the airport just before you arrived in Mammoth. We towed the 333 trailer with a flatbed F350 1999. We set it up so we could 4WD into more remote locations to do material prep and finish grinds on the skis we built off-grid. We never thought to ask why or how, we certainly didn't ask permission, but we can tell you this much. When law enforcement pulled up, some curious passerby stopped to inquire, or somebody came to do a workshop with us, the response was nearly always the same, "What the F?".
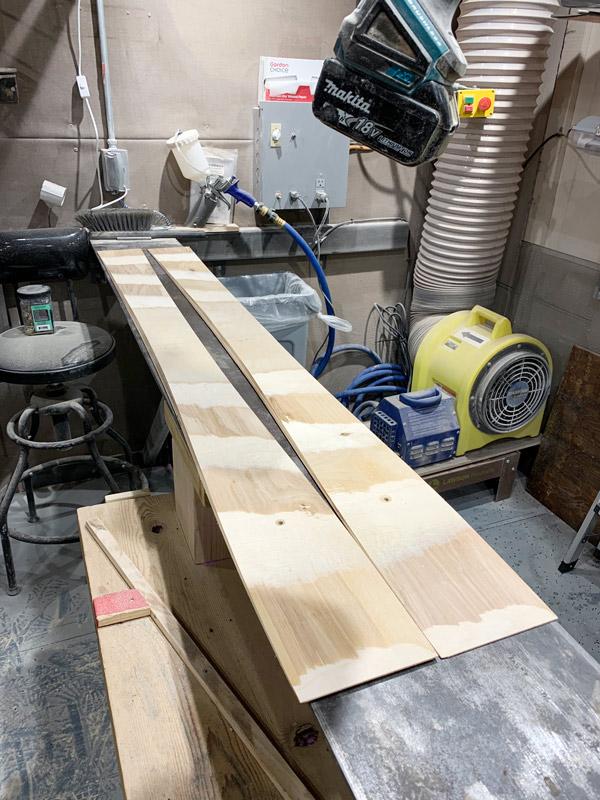
Most companies use vertical laminate core stock. It's time consuming to make, expensive, the supply chain is undependable and it is wasteful by virtue of how it is made. On the other hand, horizontally laminated 9-ply baltic birch, void free, dimensionally stable, 5x5 panels are superior in regards to torsional rigidity, consistency throughout the milling process, isless than a quarter of the price and the supply chain is dependable.
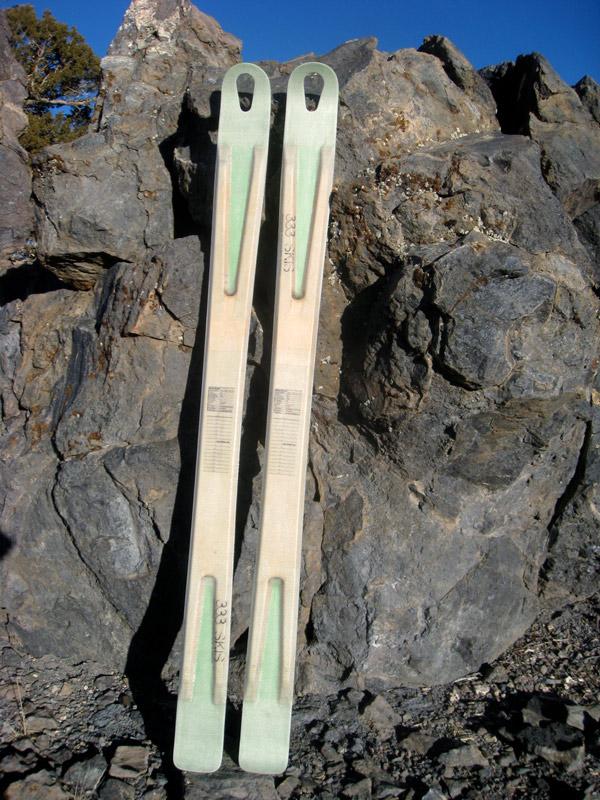
Core tapering, which is the thinning out of the core from the mid section towards the tip and/or tail, is typically done with a 1 degree average of slope. We thought, if we removed the material along the z-axis as opposed to the y-axis, we could generate flex patterns, but do something that had yet to be done; Isolating longitudinal stiffness from torsional rigidity. This allowed us to create generous flex patterns while keeping torsional rigidity (the resistance to twisting), which causes the ski to slip out of radius on a hard carve. These skis performed really well, but from here we got the idea to cut out the central web and create the deep V. As said earlier, this created an in-snow geometry which allowed for high end powder performance. Funny enough, high torsional rigidity at the tip did not seem to give us any performance gains. But that key hole, now that is something. It eliminates a high degree of deflection when skiing dense snow that has been chopped up. In other words, the snow rather than deflecting the tip, simply went through it. You just had to make sure you were not starring at your tips all the time.
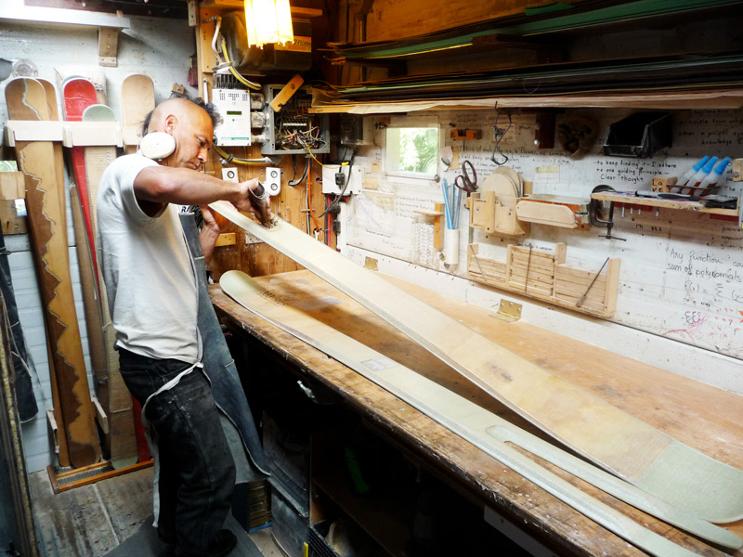
The 333 trailer was like a dream. In sub zero temperatures you could walk through that door, close it, turn on the heater and the space was so small and the walls so well insulated, that you could be in a t-shirt in about 10 mins. Turn on the stove, boil some water, make some tea and build a clients skis, or design and build a set of skis for testing you'd be on the next day. Sometimes, next day was a little tougher. The trailer could be 5' under in new snow. Kristin and I would have to break trail for up to a mile, get to the car and head up to Chair 2 parking lot, Mammoth. I'd ski like a freak. By the end of the day, Kristin and I would head back into town, do happy hour, and then trek back out to the trailer. But something that's a dream doesn't necessary mean it's a good dream. There were times when the antifreeze froze, along with the toothpaste and the eggs. One time we had a medical emergency but a thick fog had set in over Doe Ridge where we were camped in for the winter and we had a very difficult time finding our way out. But we built lots of skis, shipped them all over the world and it was a dream worth having.
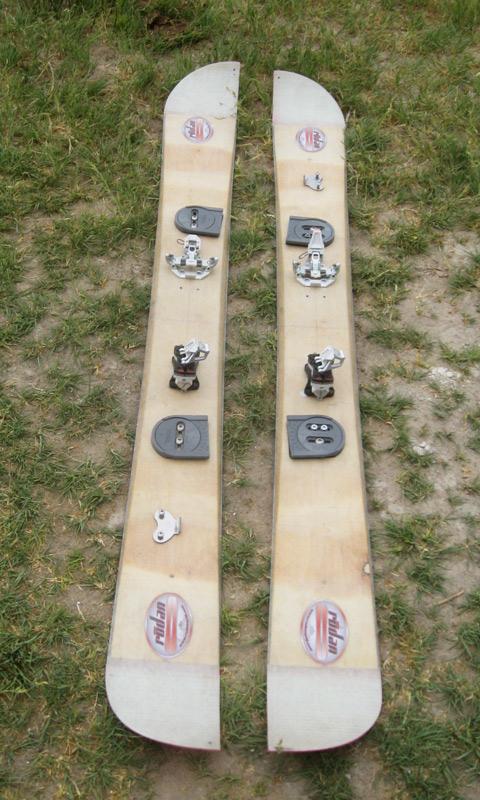
I don't remember exactly why we built this split-board. Maybe the client had 2 sets of boots he went into the backcountry with, but we built to specification and the client was happy. We've also built skis for the US Military, bush pilots in Alaska for their landing gear, snowmobile a-symmetrical runners, snow skates, mono skis for sit-down apparatuses, reverse sidecut skis, a-symmetrical skis, 200cm + double camber skis, a whole lot of mono skis, short tight radius couloir skis. We've embedded all sorts of things in skis, dollar store games, dog ashes, bud, $20 bills, glitter. So at the end of the day what do we think of all this? Each of these skis meant a great deal to the client and that meant a great deal to us.
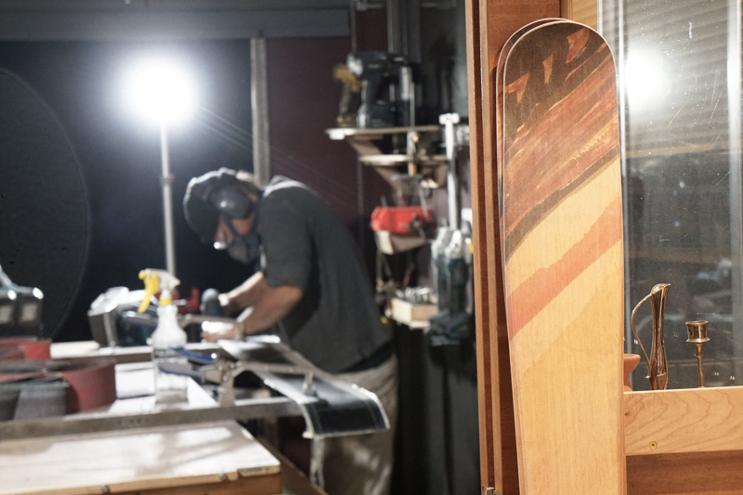
A few of the things we do requires focus of the mind. It's like a workout or eating well or being exposed to fresh new ideas that are exciting. Focusing the mind is almost like a meditation, time looses it's affect. It's a great way to spend part of your day or night.
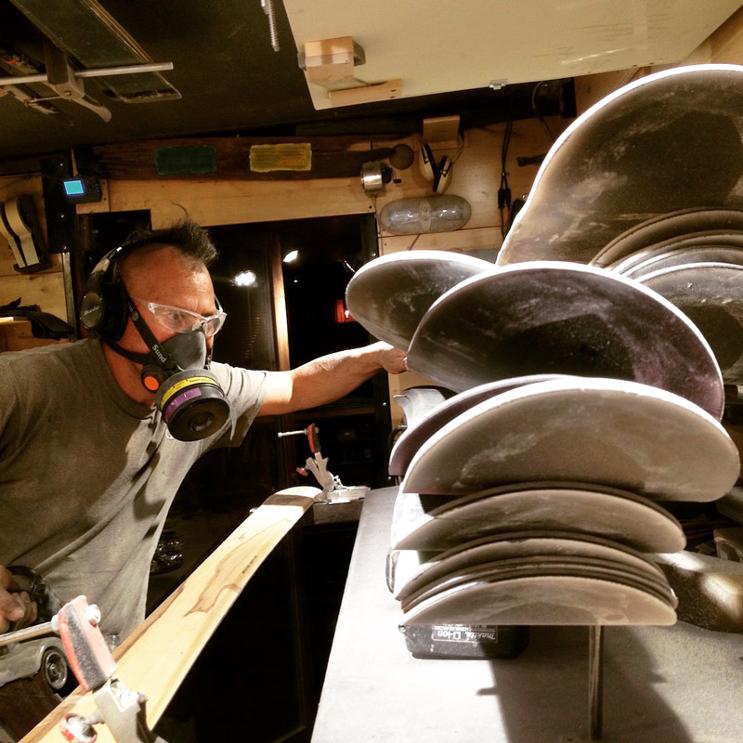
There is a battle that goes on. The love of the work vs. how much work is left to do.
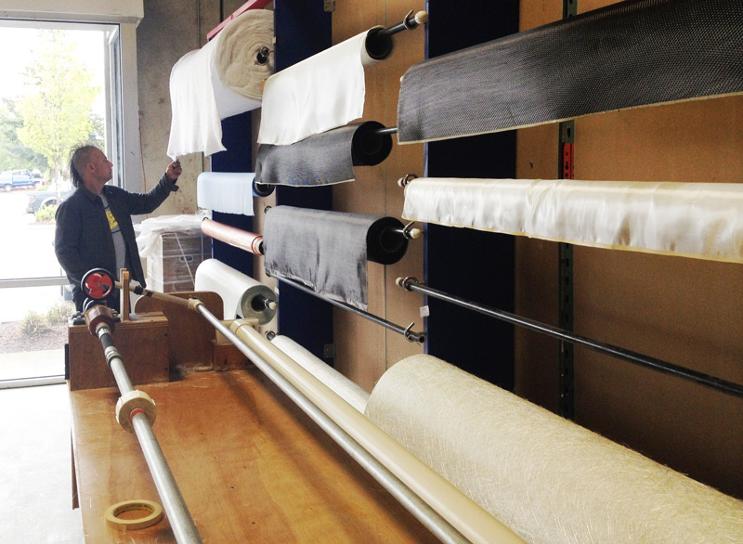
Material science is a big part of what we do. A good supply house, with a good technical staff, can give you a great deal of information which is helpful in our quest to constantly improve. You have to know that you don't know everything. So asking questions, showing up, paying attention and being open minded can make a difference.
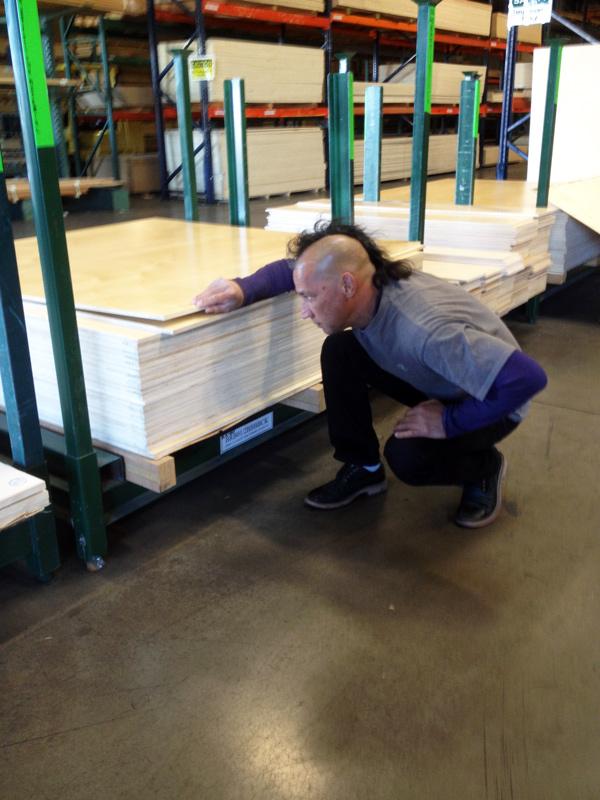
I use to wonder what the sales staff thought when this guy with a mohawk showed up. I didn't wonder in the sense, would they judge me? Would they think ill of me? Would they think I wasn't a legitimate customer? I really just thought how could I find something that we share in common and hope that they felt comfortable and optimistic talking with me. I've walked into a lot of warehouses, supply houses. At first I'm scrutinized but I get people over that pretty quick. But the real purpose is to learn what they know, go out and see and touch the materials they are working with and selling. I use to build vertical laminate poplar cores before snowboards even existed. My mother and I started a mono ski company over 30 years ago, YAMA. It was at a supply house that I learned about 9ply baltic birch, void free, dimensionally stable and off the shelf.
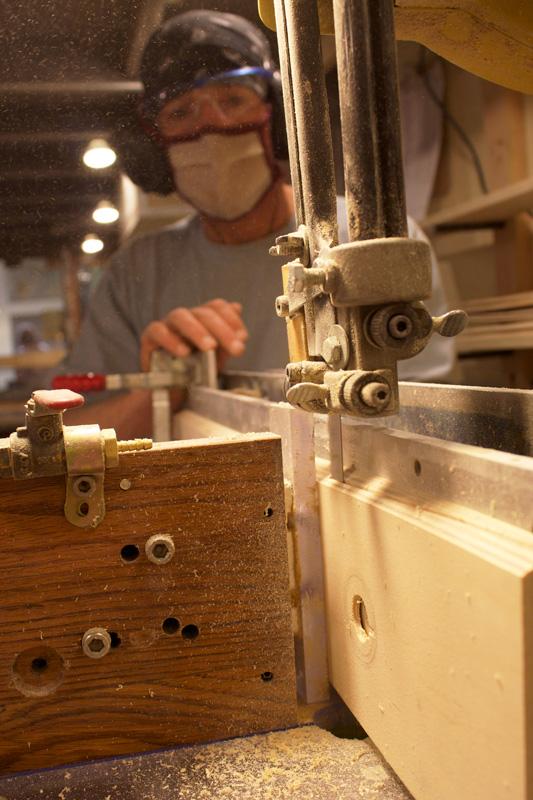
I've used chainsaws, bandsaws, planers and sanders to put the taper into the core stock. By far the chainsaw was the coolest. The wood chips flew all over the place, the bar oil smelled great, the sound was off the chart and the result was pretty good considering it was all done off-grid. But currently we're using a planer thats been modified with a carbide tip, rotary cutter that's insanely precise and extremely fast.
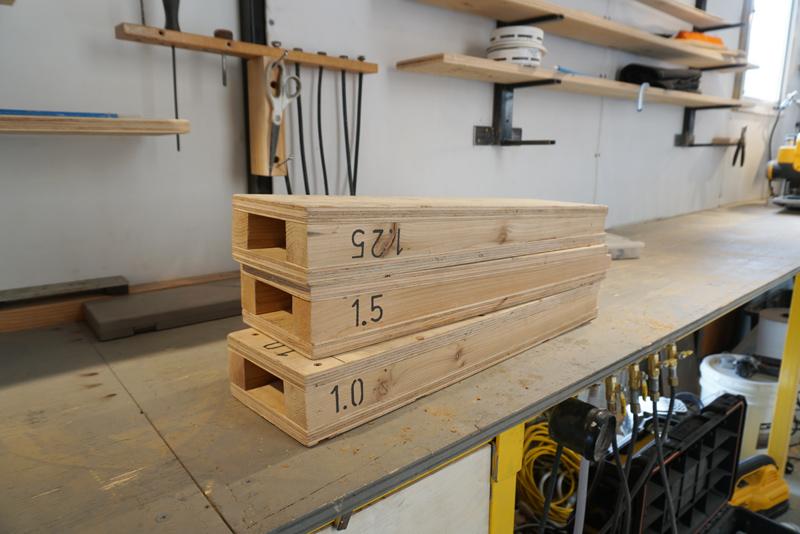
When I started making mono skis there was no internet. My mother and I went to Sun Valley, Idaho and bought a mono ski factory that was built by Mike Brunetto of RD ski fame. The factory utilized a press stack and other machinery that had come from Vachon Island (K2). The core stock was high density urethane foam. When I ran out, that's when I started researching higher performing vertical laminate cores. I went to UCLA, to the URL Library and found a book about trees. A chart came up with weight-to-strength ratios of different species. Poplar was at the top of the list for weight-to-strength. I went to a local hardwood store, they said "Yes, we have it. It is used in cabinets and it's one of the least expensive hardwoods". I figured out how to make core stock but tapering the cores was tedious and time consuming. One day I read an article in Woodworking Magazine, expaining how to taper a coffee table leg. Make a taper deck and send it through the planer along with the table leg. I swapped out the table leg for the core stock and started quickly tapering cores. The taper decks we use now are adjustable, but these are a good example of a $1.50 spent well.

This is the second reiteration of the chainsaw tapering configuration. The first one was so simple and rather elegant. This one turned into a conglomeration of sorts. I added an auto feed and switched out to an electric chainsaw. So with the push of one button, the core would self feed, taper, hit a limit switch, turn the chainsaw off and return to start location. I think I'm starring at it because I'm still intrigued, or maybe worried.
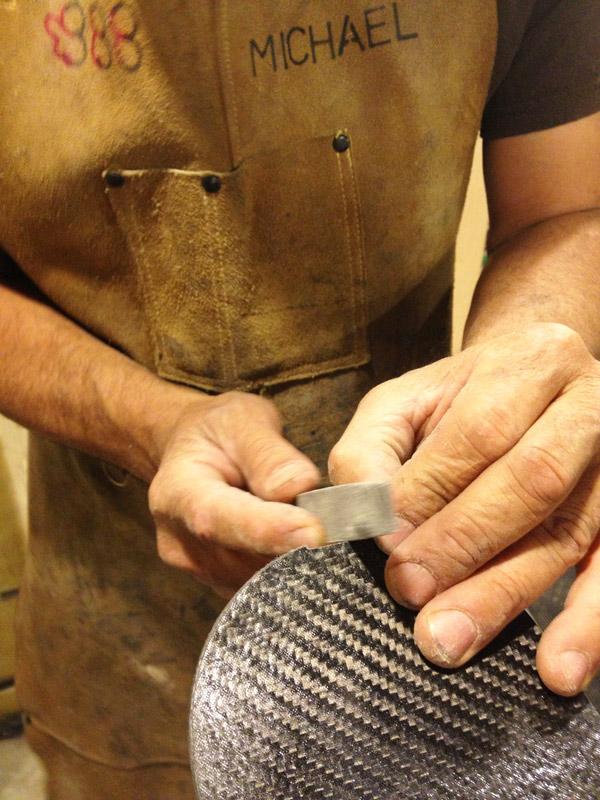
Think of all the times you've made something. Maybe you were good at it. Maybe you were not. But at least you tried and if you did it over and over hopefully you also tried to get better. So take a deep breath and look forward to your next project. Whether it is building a set of skis, building a house, or just filing a notch for skins in your AT get up.
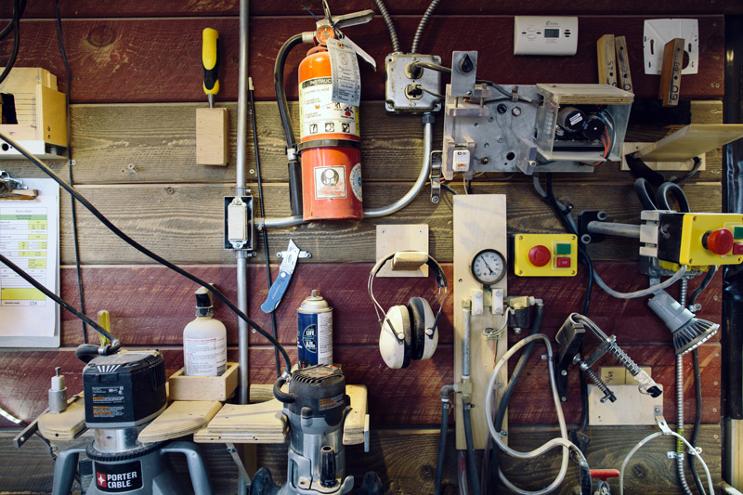
Our concern with fire is front and center. We've been fortunate, its never reared its head. But I've been told stories and seen the aftermath and a lot of the stuff we build is rather eclectic and electricity is a big part of it, so we try to make sure if a fire gets started we'll be able to put it out.
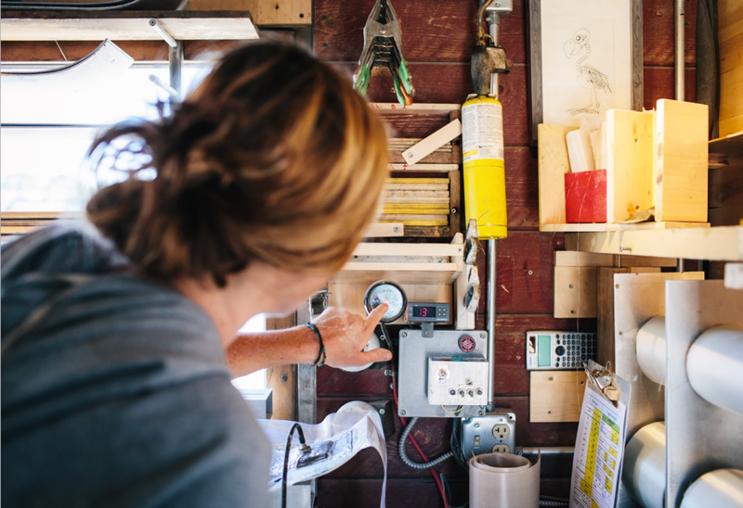
Kristin's responsibilities in many ways overlap mine, but are also distinct. She actually builds most of the skis. Equally important, she designs the graphics along side the client and manages the business. We've been partners for over 10 years, starting with 333 Skis.
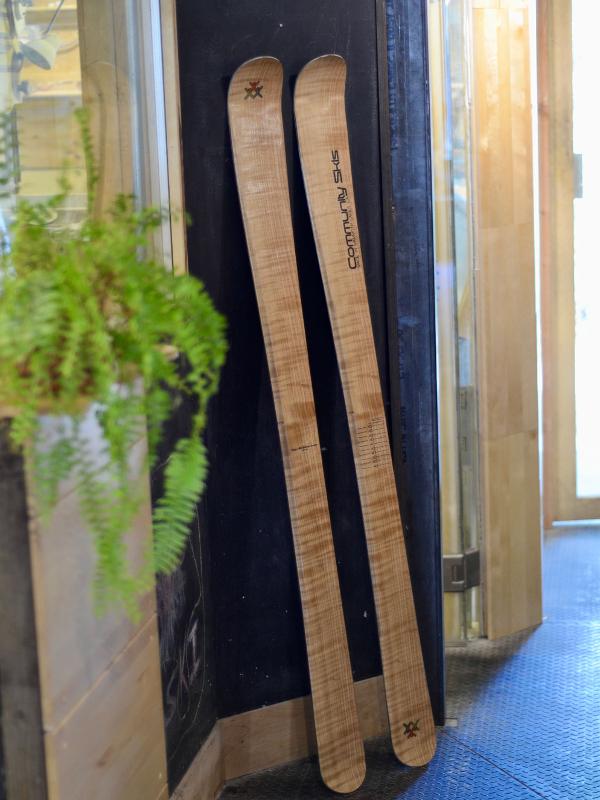
When I was building snowboards in the Canoga Park factory, two surfer guys came by and told me a story about Koa trees. They asked if we could build prototype snowboards with Koa veneer. We said yes and they came back a couple days later with some really nice graphics and a company name, Arbor Snowboards. In building the prototypes we learned how to incorporate veneer. It's a classic look and it also adds a structural component to the skis.
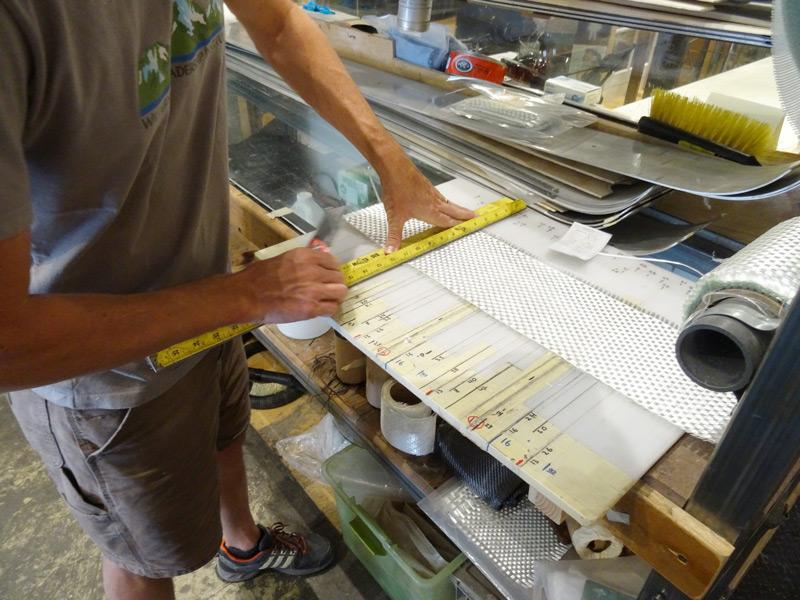
There's quite a few steps in building a ski. Our focus is on doing them efficiently, accurately and intuitively.

In the composite industry, and keep in mind that a ski is a composite, the standard is vacuum pressing, utilizing atmospheric pressure. In so many ways pneumatic pressing a ski is inefficient and costly. The presses themselves are immensely heavy and require an extensive system for regulating heat and creating even heat to be distributed through out. For doing large production runs with set parameters, they might gain some points. But take a look at this system. You can pick it up with your hand. You can daisy chain 100 skis at a time. They cure with ambient heat which is generated very inexpensively and there are infinite shapes and camber/rocker profiles that can be set in just a couple of minutes. So why do companies press skis? It really has nothing to do with the ski industry. It just turns out that most of human kind, simply follows the norm.
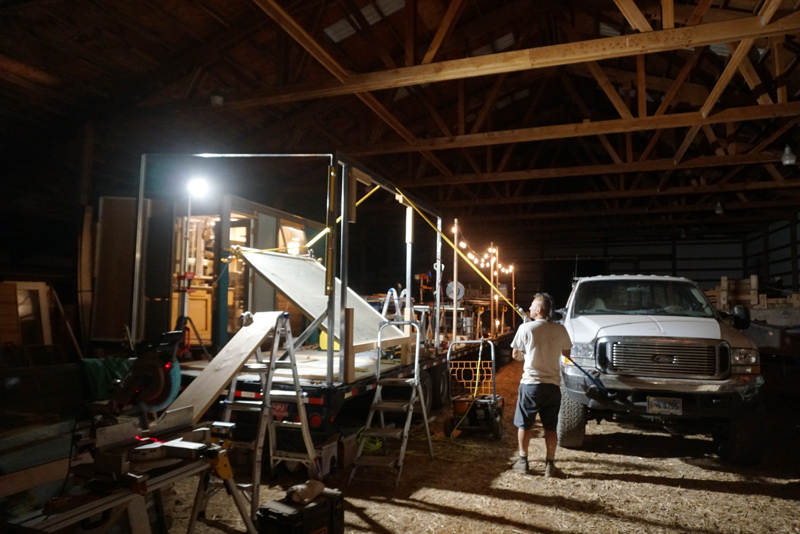
Several times through out the year we bring on an intern. Whether it is a high school student, graduate student, or someone who would like to start their own company. The rest of the time, Kristin and I work alone. This is the factory envelope for a school in Philadelphia. The classroom handles 14 students and enable them to build 14 sets of skis in a couple of weeks. The curriculum also includes an entrepreneurship program, management in a manufacturing environment, and material sciences. We use a lot of glass because these kids are like rock stars when they are working. We want people to be interested in what they are doing. To see it and encourage them.
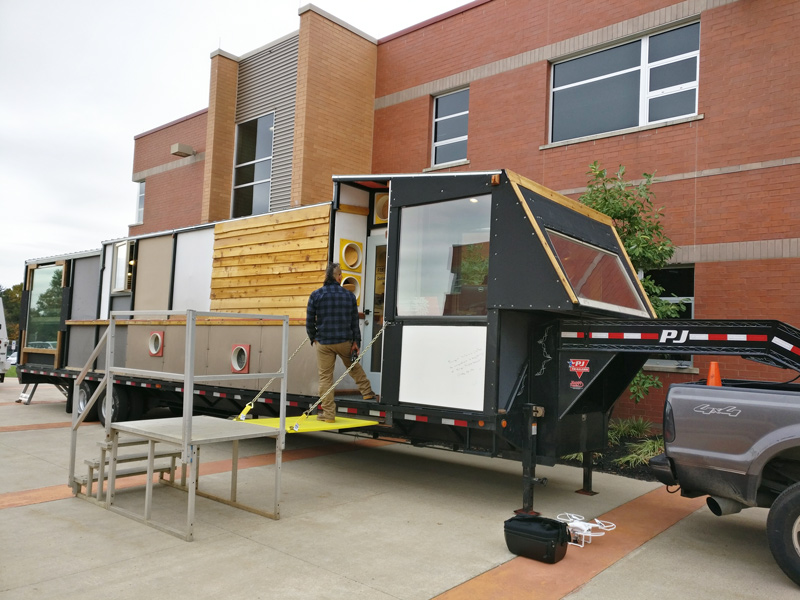
We've learned so much working with public schools. It's funny, what you initially think is not so. Bureaucracy is real and understanding it can help pave the way to successful outcomes. All in all, so much of what Kristin and I have attempted unfortunately we could not deem successful. But as they say, that was then. Now at this point we've gotten really good. But how else to have gotten here? There wasn't a road map.
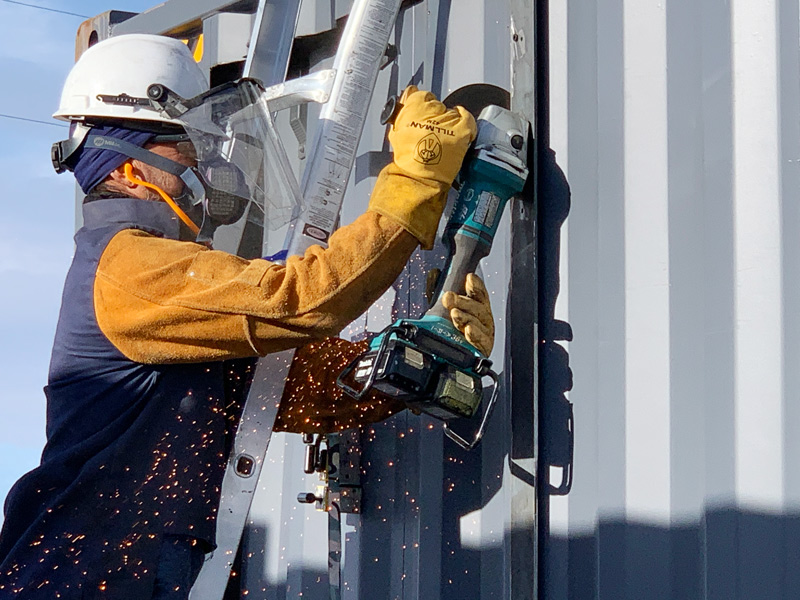
We're building a new factory. We're really excited. It has an apartment in the front section for people to stay in when they do the Build Your Own Ski Workshop, or for the intern. The structural design incorporates a 32' cantilever with expansive views and plenty of natural light. At this point it is the culmination of decades of work and our drive to be competitive, creative, innovative and remain connected to nature.
PRACTICAL INFORMATION:
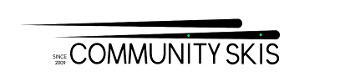
© COPYRIGHT 2024 - COMMUNITY SKIS